1. General
1.1. This safety procedures manual was written to establish consistent and multi-year standards concerning the use of fire and gas for the Midburn event.
The guidelines in this manual were written in accordance with laws, regulations, and relevant standards, primarily the document of the Australian Energy Safety Authority in the state of Victoria (which is based on reference 158 part 6.2).
"Code of Practice for the safe use of LP Gas at public events in Victoria (version 04/2015)."
Event role holders and participants shall be familiar with the procedures in this manual and will act according to them.
1.2. Section A applies to all types of work, without exception, both during the Build and Strike, (setup/dismantling) and during the event.
To avoid doubt, it is clarified that any work during the event will be carried out only after receiving appropriate approval.
1.3. Section B applies only to the operation of installations, and their care and use.
1.4. In the safety folder of each camp, all structures/facilities that will be built in the camp will be detailed. The definition of "facility" is as defined in the Israel Planning and Building Law.
1.5. Detailed instructions for setting up tents/shelters can be found in Tents and Shading Structures Build Guidelines.
1.6. All DPW volunteers, artists, and their team members, Theme Camp leaders, and those responsible for construction and safety in them, will participate in safety training that covers all the topics detailed in these guidelines and will sign for approval.
1.7. Every artist and every Theme Camp will submit to the Art Department or the Theme Camps Department, as appropriate, a signed copy of this document by all participants in the setup/construction.
2. Part A: Work Safety
2.1. Work Risks
2.1.1. Mechanical hazards (moving parts, heavy equipment, pinching, pulling, repetitive motions).
2.1.2. Fire hazard from flammable and combustible materials.
2.1.3. Risk of electrocution and laser blinding.
2.1.4. Vibrations and swinging.
2.1.5. Falling from a height, stumbling, and slipping.
2.1.6. Injury from hazardous materials.
2.1.7. Harmful noise.
2.2. General Safety Instructions
2.2.1. It is mandatory to attend safety training before starting work, tailored to the type of work, tools, conditions, and operators.
2.2.2. The work area must be marked with tape or any equivalent marking that is also effective in the dark.
2.2.3. Open pits or any other place where people might fall into, must be fenced or guarded and the Control Room (the Hive) should be notified.
2.2.4. In all work, take all precautions and use all required protective equipment according to the type of work. You are responsible for the equipment and work tools you use. Make sure the tools are intended and suitable for the job you intend to do and note that the maintenance level of the tools is appropriate and that they are functional, complete, and equipped with all required protections.
2.2.5. All machines, equipment, and vehicles in use must be registered as required by law, have a certified examiner's approval, or any other license, including the Ministry of Transportation.
2.2.6. Any driving, work, and/or operation of a device/machine should be done by someone with a suitable license/approval.
2.2.7. It is obligatory to resent all required permits and licenses according to law or regulation. Failure to present the permits and licenses might delay the execution of the work.
2.2.8. Do not handle a "moving" system or tool before checking that the energy/power supply is disconnected.
2.2.9. Use lighting during the dark (ambient lighting and sufficient local lighting).
2.2.10. Manual tools should be intact and functional.
2.2.11. Before starting work, make sure there is a 6kg fire extinguisher or other fire extinguishing means in the work area.
2.2.12. A participant should not start, and if started, should stop any work that seems dangerous or risky and immediately notify the safety officer in his department/work team.
2.2.13. Do not block:
· Traffic routes and passages for vehicles and pedestrians with equipment, work tools, or vehicles.
· Evacuation routes, fire extinguishing stations, extinguishers, electrical cabinets, and emergency electrical disconnect switches.
2.2.14. Wear a hat in the sun, drink plenty of water to prevent dehydration, use sunscreen, and wear warm clothing in cold/windy conditions.
2.3. Clothing and Personal Protective Equipment (PPE)
2.3.1. All those engaged in work should wear work clothes according to the work performed and closed shoes.
2.3.2. Gather hair and loose clothes, and do not wear hats/scarves when working with/near machines, tools, or facilities with moving parts, or near a fire source.
2.3.3. In addition to basic PPE, additional protective equipment should be used according to the type of work, such as: protective helmets in welding/construction/high-altitude work areas, earplugs/earmuffs in noisy areas, protective glasses when using hazardous materials/painting/polishing or any other work that creates dust or chips, respirators, face shields during cutting with a disc/grinding, etc., and work gloves.
2.4. Preventing Fire / Using Hot Equipment
2.4.1. When performing hot work (cutting, welding...), there should be a 6kg extinguisher on site.
2.4.2. Remove all flammable materials before starting work. Material that cannot be removed should be covered with a fire-resistant cover/wetted with water.
2.4.3. Do not fuel generators while they are operating; shut down the generator before refuelling.
2.5. Electrical Work
2.5.1. Electrical cables should be intact and functional and have circuit breakers; keep electrical cables away from water sources and other liquids.
2.5.2. Do not perform electrical work when the cables are charged (connected to a source).
2.5.3. Electrical work (except for standard "plug-socket" connections) should be performed by a certified electrician only.
2.5.4. In case of electrocution, turn off the main switch and/or move the person away from the electrified equipment using a wooden stick or an insulated object.
2.5.5. Do not touch an electrocuted person with bare hands.
2.6. Lifting Work
2.6.1. Lifting work should only be performed using lifting devices and machines equipped with a valid approval from a certified examiner and operators certified to operate them, who have valid approvals.
2.6.2. A mobile crane should be operated by a certified crane operator.
2.6.3. Only operate a forklift or a mobile telescopic lifter with a certified and experienced operator familiar with the tool he is supposed to operate.
2.6.4. Do not move lift devices when a telescopic arm or a lifting device is at a height.
2.6.5. Do not lift people with a forklift, only with a standard lifting basket approved by a certified examiner.
2.6.6. The liftting machine operator is responsible for ensuring that no one is under or near the path of a lifted load during the lifting process (including lowering and transferring loads).
2.6.7. When lifting a heavy weight (over 20kg) without mechanical aids:
2.6.8. Use another person or a cart.
2.6.9. Plan the lifting method and path.
2.6.10. Correct lifting procedure steps:
a) Lift slightly to gauge the weight.
b) Stand close to the equipment, feet on the ground.
c) Sit down, back straight, knees bent.
d) Embrace the equipment and try to lift it.
e) Rise using the knees slowly with a straight back.
f) Hold the load close to the body, ensuring a clear field of vision.
2.7. Work at Height
2.7.1. Any work performed at a height above 2 meters requires the use of a full safety harness (do not use a safety belt).
2.7.2. Every work at height worker should present a valid training certificate suitable for the type of work.
2.7.3. Work according to work at height guidelines:
2.7.4. Ladders - only use standard ladders. Ensure that the ladder is anchored properly. If there aren't 3 grip points, connect the safety harness to an anchoring point. Use helmets with chinstraps.
2.7.5. Scaffolds - every scaffold must meet all safety requirements and be fenced according to work safety regulations. In some cases, it requires approval from a certified examiner.
2.7.6. Motorized lift platforms - whenever there's a need to work with a lift platform (like a BOOM LIFT), or use forklifts and cranes, ensure before starting work that all required approvals exist (certified examiner for the machine, licenses for crane operators, forklift driving license, and any other required approval).
2.7.7. Fence the work area to prevent workers from passing under the area where the work is performed.
2.7.8. Move the lift platforms with a guide from the ground.
2.8. Hazardous Materials
2.8.1. Any material that is not water is defined as a chemical.
2.8.2. Such material has the potential to harm health and the environment when control is lost during work or storage.
2.8.3. Chemicals can be physically harmful to the body acutely and chronically.
2.8.4. Chemicals enter the body through inhalation, penetration, ingestion, and absorption.
2.8.5. Some risk groups: poisonous, oxidizers, solvents, corrosives, and compressed gases.
2.8.8. Only dispose of chemicals in a predetermined, authorized spot
2.8.9. In case of being splashed with a chemical, remove clothes and wash self for 15 minutes, then seek medical treatment.
2.8.10. Be aware of the risks and required safety measures when working with a chemical. Be aware of the specific fire extinguishing procedure – act according to the SDS (Safety Data Sheet).
2.8.11. An SDS (Safety Data Sheet should be attached to every hazardous material.
2.9. Emergency
2.9.1. Any emergency event (fire, casualty, injury, electrocution) should be reported to the coordinator who will update the producer and all relevant individuals, and if necessary, the clinic as well.
2.9.2. In the case of a fire, try to extinguish it only if it can be done without personal risk, using a fire extinguisher only. In the case of electricity - use a powder extinguisher only.
2.9.3. In the case of injury from any chemical, rinse the affected area for no less than 15 minutes, including in cases of eye exposure.
2.9.4. In the event of an injury resulting from a blow or fall, do not move the injured person until a certified professional arrives!
3. Part B: Operation and Use of Installations/Facilities
3.1. Moving Parts
3.1.1. If the installation or facility incorporates moving parts, mark the moving section, and physically prevent (e.g., barrier, fencing, elevating) access to moving parts that could harm event participants or the setup team or camp team.
3.2. Installations or Facilities that Incorporate Climbing and/or Manual Operation
3.2.1. Any installation, facility, or structure that integrates a physical activity of event participants might require supervision during the activity time. Installations/facilities that require supervision during activity will be prevented access when there is no supervisor and will be visibly marked accordingly.
3.2.2. Marking the installation/facility: Prominently mark on a large sign how many people can use the facility or structure at one time or signage indicating "Climbing Prohibited", as well as any restrictions on use, as determined by the safety engineer.
3.3. Installations or Facilities Not Intended for Climbing
3.3.1. Place a sign stating: "Do Not Climb" prominently and prevent access as much as possible.
3.4. Anchoring Installations/Facilities
3.4.1. Installations/facilities must be anchored well to prevent movement of the installation/facility.
3.4.2. Builders of high installations, facilities, or structures must consult with a structural engineer/mechanical engineer during the planning phase.
3.5. Marking Installations, Facilities, and Anchors
3.5.1. Installations should be marked prominently so that they’re visible both day and night.
3.5.2. Mark ropes and anchors to prevent injuries. Sharp nails and metals should be covered as much as possible.
3.5.3. Installations and facilities that incorporate nighttime activities should ensure adequate lighting.
3.6. Electricity in Installations and Facilities
3.6.1. Installations and facilities that incorporate electricity should ensure that all cables are intact, and that there's no contact between electrical parts and metal. These installations should be equipped with a safety switch and a quick electricity disconnection capability.
3.6.2. Installations operating at a voltage above 50 volts should be inspected by an electrician before activation.
3.6.3. Structures and facilities in Theme Camps that incorporate electricity should be inspected as part of the camp check. For additional safety instructions regarding electricity in theme camps, refer to the Electricity Guidelines.
3.7. Installations or Facilities Incorporating Fire (excluding burning the installation)
3.7.1. Ensure all parts of the installation are fire-resistant and do not contain flammable, combustible, or toxic materials. Keep flammable materials away from the installation.
3.7.2. Do not leave a burning fire without supervision.
3.7.3. As a rule, do not light a fire in the camp except in a designated area (kitchen, and according to guidelines in the fire use guidelines). In other cases, consult with the Safety Department.
3.7.4. For additional safety instructions regarding the use of gas, refer to the Gas Stove Guidelines
3.8. Safety Defects Identified in Installations and Facilities
3.8.1. If safety defects that endanger the well-being of participants are discovered in an installation/facility, access to the installation should be prevented and prominently marked. The installation/facility will reopen after correcting the defects and checking with the safety consultant.
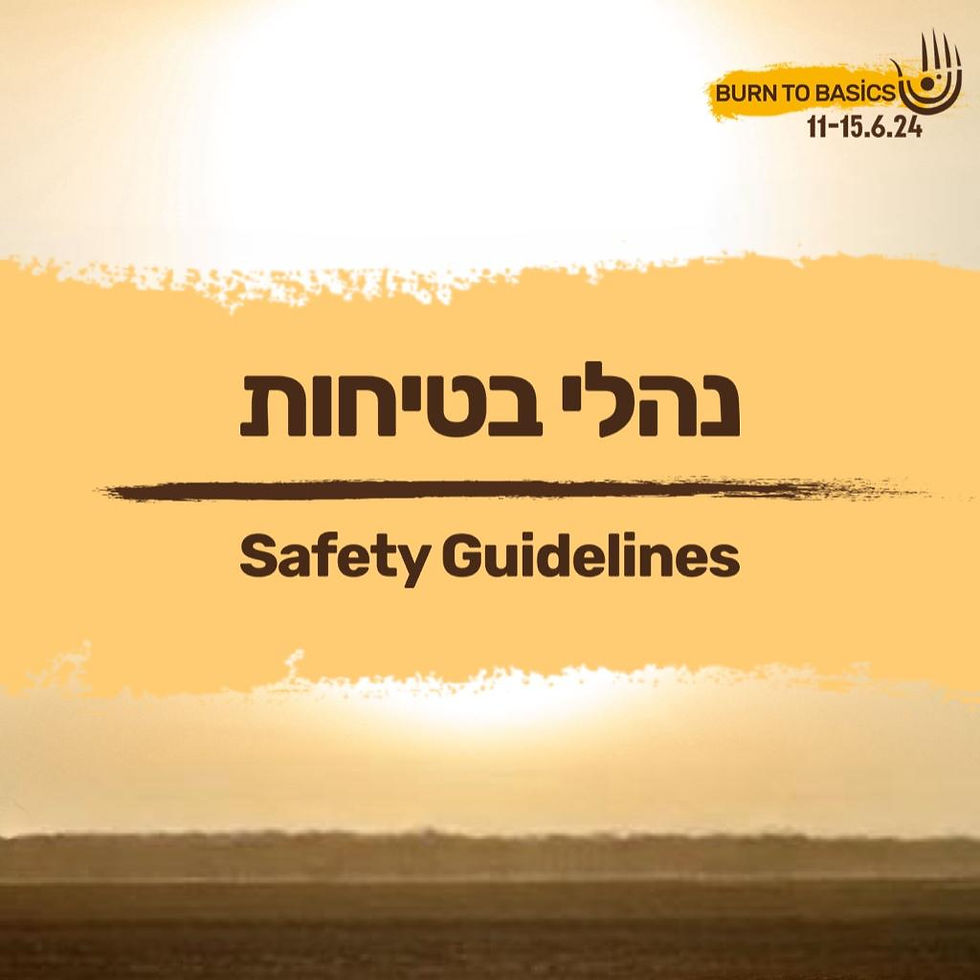
Comments